Pre-Shipment Final Inspection
Pre-Shipment Final Inspection
5.0 / 5.0
(24) 24 total reviews
Simple. Free. Advice. No Obligations.
Couldn't load pickup availability
Imagine the cost of receiving a container of damaged or faulty goods from China.
Would you risk paying your Chinese manufacturer for products only to find out they are all wrong?
Pre-shipment final inspection is for every buyer who needs to ensure the factory has produced their goods according to all their requirements with good quality before the goods leave the factory in China.
Not receiving what you are expecting is a serious problem. But that's not all it takes to stop defective goods from shipping.
What makes this even worse is the fact that you risk paying your Chinese suppliers before verifying your quality and commercial requirements have been met! This means you risk paying for and receiving goods that you cannot sell.
The biggest mistake we see many buyers unintentionally make is assuming everything they confirm via email or messaging will be filtered down to the factories' production lines.
All this can make trying to prevent problems before goods leave the factory a nightmare! But luckily for you, we are here on the ground in China to help you!
So, if you're a buyer who really needs to ensure the factory has produced your goods according to all your requirements with good quality, our "Pre-shipment final inspection" is what you need!
Getting started and figuring out how we can help you (everyone has a different need) couldn't be easier as you can schedule a free call now below, and let us figure it out for you.
HOW IT WORKS
-
You submit whatever documents you have via our online form.
-
We review and build your "quality control checklist" for you to sign-off.
-
You or your supplier book the inspection via our online form.
- We do the work and report back to you.
BENEFITS
FACTORY PRESENCE! Having our staff on-site provides you the ability to have someone physically checking and testing your goods on-demand within 24 hours.
VIDEO & PHOTO! Lets you, from the comfort of anywhere, see your goods being checked, used, and tested with all their packaging, labeling, and anything else you asked for before they leave the factory. Same day!
ANYWHERE IN CHINA! No matter where in China your factory is, you pay the same price and can have someone on-site within 24 hours. Effortless!
QUALITY CHECKLISTS! Your products will be checked for quality, performance, and construction to ensure they are fit-for-purpose and will last a long time. We will build a quality checklist for you. In a snap!
ORDER CONFORMANCE! We also go above and beyond quality checks to assure you that any of your commercial, contractual, marking, packaging, or other requirements have been adhered to by the factory. A comforting thought!
FREQUENTLY ASKED QUESTIONS
What information do I need to provide?
You will be requested to provide any purchase orders, product sheets or invoice copies, compliance certificates, artwork sign-offs, etc., that contain details of your order. We will use whatever you can provide to create your quality plan (checklist). If we have done Order Management for you, we will automatically do this for you as we already have all the information. You might only have a simple one-page purchase order, and that is perfectly ok.
Why do you inspect?
We inspect to ensure no mistakes or human errors occurred during the production or communication steps at the factory. It is a safeguard that saves costly reworks or stop-sales in your home country.
If my goods are inspected, does this mean the quality is perfect?
It is really important to understand that one cannot "inspect quality into a product". Quality and reliability is inherent from design to process, and incorporates aftermarket feedback. Quality is a continuous improvement cycle. Inspection can detect a considerable amount of potential problems and reduce risk substantially but it cannot guarantee quality or reliability. Feel free to schedule a free call to discuss in more detail, if you feel you require more comprehensive reliability, laboratory or verification testing. Our goal is to design the most suitable quality plan for you.
What is a PSI?
It is a pre-shipment inspection. This is to test products after mass production and ensure they are suitable for sale, and meet all your requirements before the goods leave the factory.
What is the sample size?
This is the number of pieces we will check from your production. There are international standards that are used, and we will recommend the most appropriate to you. We use what is known as an AQL table to determine the sample size.
Do you need a perfect sample before you do inspections?
This is referred to as a golden sample. Our rule of thumb is YES. It is best to work with a golden sample to avoid subjective findings. However, in cases where this is not possible, we will have you confirm and acknowledge this, and set criteria for decision making, with any subjective findings being referred to you for a final commercial decision.
Do you only look at technical and functional aspects of quality?
No, we check any requirement you have, whether it be technical or commercial. Our philosophy is to inspect what you expect!
Will you check my packaging and labeling?
Yes of course.
Do I need to tell you what quality checks to do?
No, our team will propose a detailed quality checklist, which you can freely amend and add to as you see fit.
What tests do you perform on my products?
We offer all kinds of quality checks, such as drop tests, rub-off tests for printing, fade tests. We usually divide tests into different categories; 1) Function and performance; 2) Internal construction; and 3) Conformance to purchase orders. We also check non-quality related items that are commercial requirements you may have agreed with your supplier, or design and packaging requirements you signed-off on.
What if my inspection fails?
Don't be alarmed. It's not uncommon. In fact, you want problems to be identified before the goods depart. Typically, you have a few options: you can choose to accept the finding (commercial release), have the factory re-work the issue, or in some cases negotiate a discount. Our team and their experience will guide you through the decision-making process, and provide you with some valuable resources on how to ensure improvements are made and problems prevented in the future. Our team will also help you liaise with the manufacturer for corrective actions.
Do I get an inspection report?
Yes, you will get a detailed report with a summary, including videos and images, and our own internal conclusion.
What other types of inspection are there?
We can do an Inline Inspection (which is done during production of the goods, not after they are complete), and we can do a Container Loading check to ensure the goods are safely packed in a damage-free container.
Listen to these podcast episodes
Some Avoidable Costly Mistakes When Sourcing From China | Ep. 021
What To Do When Product Inspections Fail | Ep. 025
Accountability - Who is Ultimately Responsible? | Ep. 027
If you have any doubts or questions the quickest solution is to schedule a free call below.
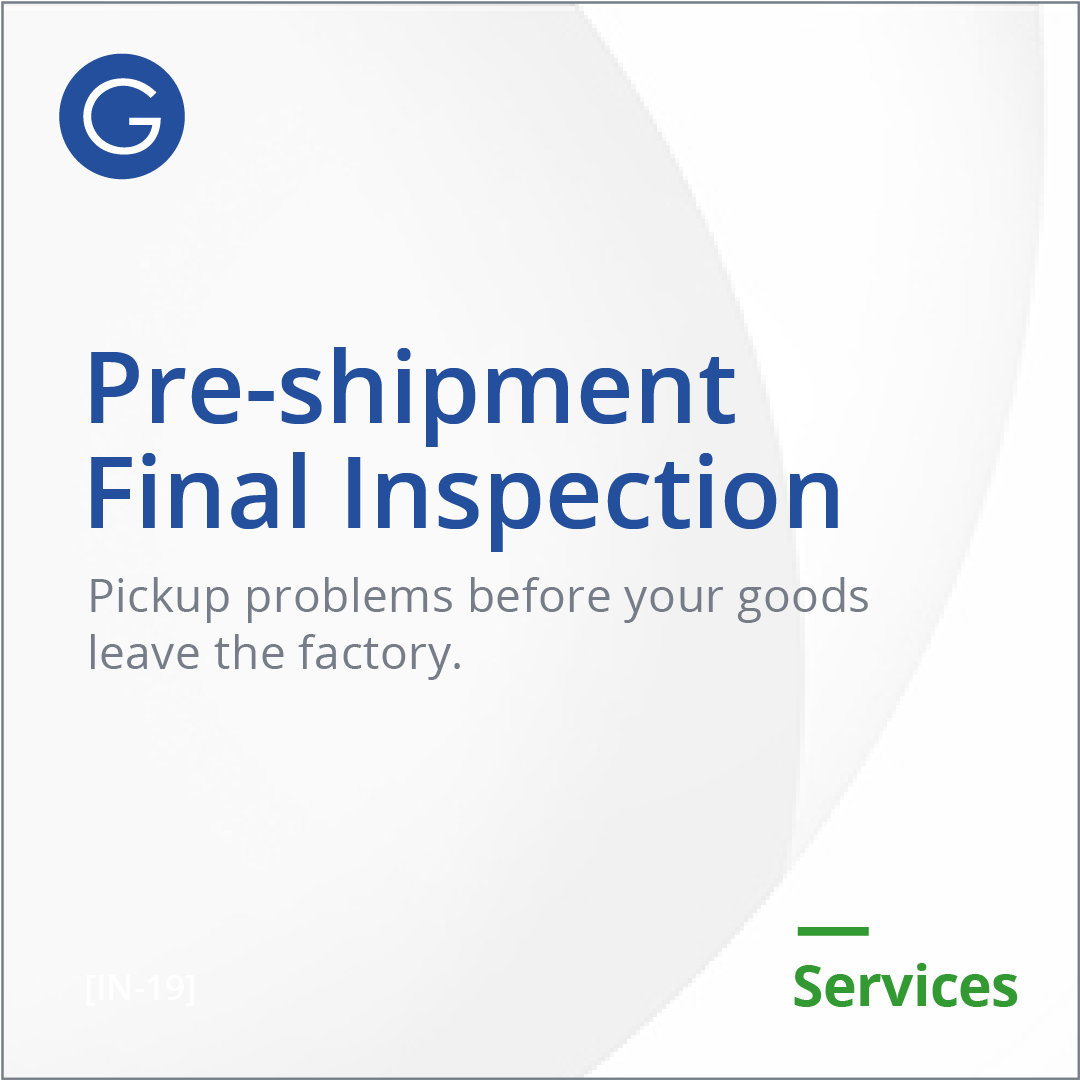